Bosch VP44 Injection Pump Failures Explained
- Blue Chip Diesel
- Feb 12, 2018
- 3 min read
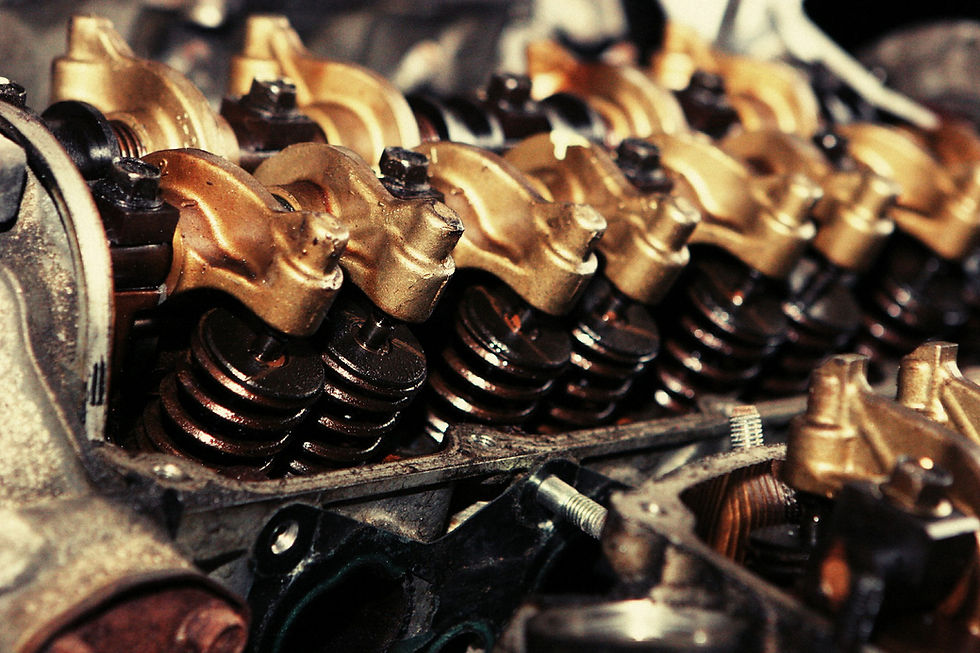
The best way to start this explanation is to quote an e-mail that I found on the corporate Cummins website many years ago. “The Bosch VP44 has not been as reliable as we had hoped.” We have dismantled many pumps to figure them out and diagnose what failed and what the cause AND SOLUTION is for the failure. We think you might like to hear about our findings.
A common problem with original pumps in 1998 through 2000 trucks, is the rotor seizes in the distributor section of the pump. This is also common in rebuilt pumps that don't have the upgraded rotor, distributor and coating. This is why engines just die going down the road, usually when the throttle is released at high load and or high RPMs, and never start again until a replacement injection pump is installed. We should note here that all rotary pumps have this potential problem, to varying degrees, so this is nothing new to the injection pump world.
What actually happens when the rotor seizes, and this is from a Bosch Factory Rep, the slot in the rotor interferes with the distributor because of an inferior deburring process. In layman’s terms “deburring” is eliminating sharp edges. As a sharp edge isn’t strong, it deflects under the 4600-PSI inside the pump. The sharp edge deflects and interferes with the distributor and galls both mating parts and then seizes. The drive plate then breaks and only the input shaft of the pump rotates, so no high pressure fuel is delivered to the injectors.
The computer on the top of the injection pump is the most common component to fail and causes many different symptoms, as explained in our diagnostic pages. This component fails due to "Lead Free" solder that secures the components to the circuit board. The use of this kind of solder is mandated by the Federal Government's EPA division. Heat and heat cycles make the solder crystalline over time and create an intermittent electrical connection, which makes the pump do all kinds of naughty things.
The old style diaphragm can cause hard start cold, as it cracks over time with prolonged low lift pump pressure, and can be diagnosed with our diagnostic pages.
As these pumps are getting older and the cores have more miles on them when we get them, we are learning of other components that just plain wear out and cause problems, such as the rotor and distributor. There is no good way to test them, either mechanically or on the useless test stand, so sadly the end user gets to do the diagnosis more often than not. The result of a worn out rotor and distributor is a hard start hot, also explained in our diagnostic section.
The famous 216 code that some vendors tell you is a death code for the VP44, is NOT. All it is telling you is that the timing is not advanced as much as the ECM wants for more than 5 seconds. This can be caused by low lift pump pressure or a worn out housing on the injection pump. If you have good lift pump pressure UNDER LOAD and that code keeps coming back after you clear it, then you know the pump is getting tired, but that code alone does not tell you the engine is going to die soon and put you on the side of the road, as some vendors want you to think.
There have been a bunch of mechanical and electronic upgrades for these pumps made available from Bosch, and they have proven to be much better than those used when this pump was originally made. The mechanical upgrades have all been a winner in my experience. They seem to last a long time and are surely worth using in a rebuild scenario, but they cost money so when the typical rebuilder is trying to save money in a typical rebuild, they just aren't used.
This is where Blue Chip Diesel is different. All of our pumps have all of the mechanical and electrical upgrades on them. See our "Products" page to learn about the many pump choices you have when doing business with us!